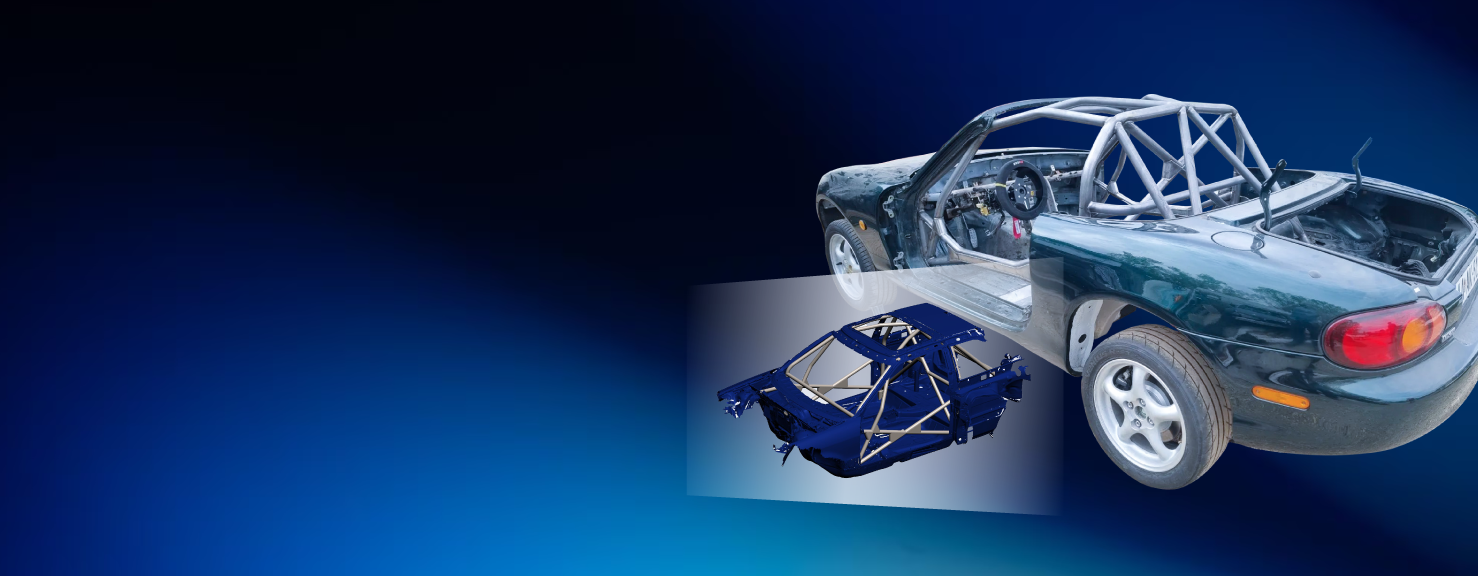
CASE STUDIES
Published on Jun. 25th 2025
Application and Advantages of 3D Scanning in Roll Cage Design
Facing rising demand and stricter standards, DriftGarage, an FIA-certified roll cage producer since 2017, partnered with Modception to streamline production. Using FreeScan Combo Series and CAD design, the process enhanced precision, cut labor hours, and delivered superior roll cages.
Facing rising demand and stricter standards, DriftGarage, an FIA-certified roll cage producer since 2017, partnered with Modception to streamline production. Using FreeScan Combo Series and CAD design, the process enhanced precision, cut labor hours, and delivered superior roll cages.
What is a Roll Cage?
A roll cage is a critical safety feature in motorsports, designed to protect drivers and enhance vehicle performance. This frame-like structure typically includes a main or side roll bar, a front roll bar, rear supports, and connecting components. Beyond reinforcing the car's body for added rigidity, the roll cage plays a key role in safeguarding drivers during collisions by absorbing impact forces and minimizing injuries. Additionally, it provides stability at high speeds, reducing the risk of rollovers and ensuring safer racing conditions.
Traditional Way to Build a Roll Cage
Creating roll cages traditionally relies on manual processes, starting with measurement and design. Key car body dimensions are measured using basic tools like tape measures and calipers, followed by preliminary designs crafted in CAD software. Next comes material selection and cutting, where high-strength, lightweight steel or aluminum tubes are chosen and manually cut to specified lengths using cutting machines or saws. Afterward, tubes are bent manually to fit the car's interior, welded to the body, and adjusted for a secure fit. Finally, the roll cage undergoes professional inspection to ensure compliance with safety standards.
However, the manual process often requires repeated adjustments and is far from convenient. In addition to being time-consuming and labor-intensive, traditional methods have notable drawbacks:
- Accuracy Issues: Manual measurement and bending can result in errors, particularly with intricate designs, compromising safety and fit.
- High Dependency on Expertise: The process relies heavily on experienced technicians, introducing variability in quality.
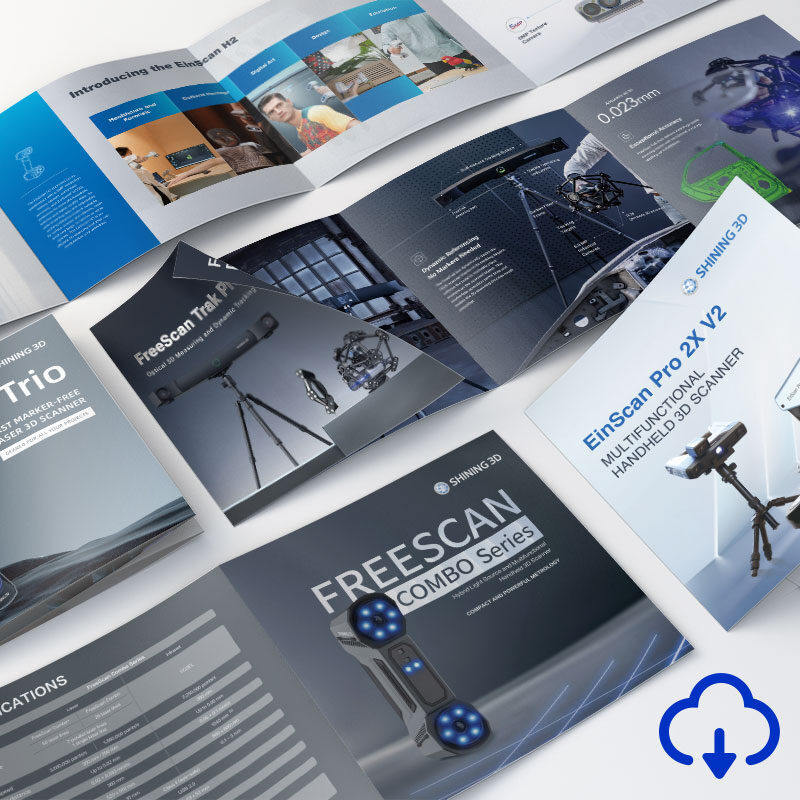
Discover the product you're looking for
- Full specifications
- Using scenarios
- Key features
- Even comes with a bundle!
Application of 3D Scanning in Roll Cage Production
Lajos Turi, founder of Modception and a veteran in motorsport customization, utilized SHINING 3D FreeScan Combo Series for roll cage production. By leveraging 3D scanning technology, the process achieved greater accuracy, reduced manual adjustments, and improved overall efficiency, ensuring the roll cages meet stringent industry standards.
Here’s a look at the full workflow.
1 Preparation
Seats and trim are removed to expose the metal frame. If needed, nearby suspension parts are disassembled. For laser scanners like the FreeScan Combo, surface spraying is typically unnecessary, as the scanner can capture data directly from most surfaces. To ensure accurate alignment, markers are then applied to the car's interior.
Remove the interior components to expose the metal framework
2 Scanning &Processing
Lajos recommends scanning the car in distinct sections, as this method offers several benefits:
- It reduces the demand on computer resources, ensuring smoother scans.
- It helps avoid errors in tracking, which could cause the entire scan to fail if the initial mark scan is missed.
For areas like the strut towers in the engine compartment, the scanning starts from inside the car and moves outward, ensuring all key parts are captured accurately.
With global markers, scans align automatically and can be directly meshed. The data is then aligned to a coordinate system, cleaned, and simplified for CAD use.
3D data of a car
3 Modeling and Design
Once the 3D data of the car is imported into the design software, the roll cage template is placed and adjusted for optimal fit. The welded tubes are positioned to balance strength and driver space. Key connection points are reinforced with custom parts to distribute loads evenly across the chassis.
Roll cage modeling and design
4 Roll Cage Production
Once the design is approved, the sheet metal parts are exported for laser cutting, and the tube model is processed using Bend-Tech software. This software generates cutting and bending instructions, allowing DriftGarage to manufacture the tubes, which fit perfectly on the first try without physical fit checks.
Roll cage
Advantages of FreeScan Combo Series in This Application
- Increased efficiency: FreeScan Combo Series speeds up design and manufacturing by eliminating cumbersome setups and enabling faster data capture.
- Reliable accuracy: Advanced scanning technologies and feature tracking ensure precise fit and alignment for complex parts.
- Cost effectiveness: Reduced setup and scanning time lead to lower production costs and fewer revisions.
“My workflow got way faster, much more precise, my scan data got so good that I can blindly rely on it and they never let me down. Now that I had the opportunity to try Combo I could get a glimpse on what the difference is between the professional and metrology-grade scanners, how much faster and better it can still get with higher grade tools.”
-- Lajos Turi
Conclusion
By integrating 3D scanning technology, Modception significantly improves the design and production of custom roll cages. FreeScan Combo Series' efficiency, accuracy, and flexibility streamlined the workflow, reduced setup time, and ensured perfect fitment. This enabled DriftGarage to produce high-quality, FIA-certified roll cages faster and more cost-effectively, ultimately enhancing both safety and performance in motorsports.
Would you like to integrate 3D scanning into your workflow? Contact our engineers for information and guidance or visit our FreeScan Combo Series page to learn more.
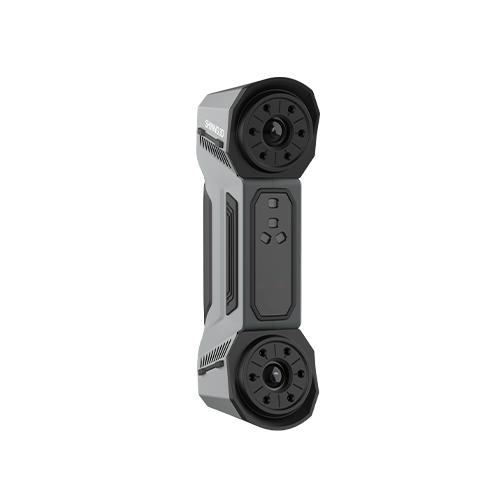
FreeScan Combo
The powerful FreeScan Combo packs dual light sources in an ultra-compact shell, measuring just 193x63x53mm. It's equipped with both blue laser and infrared VCSEL technology and weighs in at only 620g.
- Blue laser & Infrared light
- 4 Scanning modes to cover all types of workpieces
- Lightweight